Der Boden ist das meistbeanspruchte Bauteil eines Gebäudes. Genauso vielfältig wie die industrielle oder gewerbliche Nutzung der Gebäude ist auch die Beanspruchung der Bodenflächen. Für den Fall, dass der Estrich oder der Betonuntergrund diesen Belastungen nicht gerecht werden kann, ermöglichen speziell entwickelte Bodenbeschichtungssysteme auf Kunstharzbasis einen optimalen und dauerhaften Schutz des Bodens. Dieser Beitrag gibt einen Einblick in die Vorteile von Bodenbeschichtungssystemen und geht auf deren Komplexität und ausgewählten Eigenschaften ein.
Bodenbeschichtungen: Warum überhaupt, und was muss beachtet werden?
Böden müssen auftretende Belastungen zuverlässig auch über lange Zeiträume hinweg aufnehmen und ableiten können. Diese Anforderungen erfüllen in vielen Bereichen herkömmliche Zementestriche oder Betonbodenplatten. Es gibt jedoch Einwirkungen, die die Dauerhaftigkeit solcher Untergründe in Frage stellen. Häufig spielt die Porosität des zementgebundenen Werkstoffs eine Rolle, denn die Festigkeit und der Verschleißwiderstand werden hierdurch limitiert und flüssige Substanzen können eindringen. Je nach Medium können die Hydratationsprodukte geschädigt werden, was die Qualität des Untergrundes mindert und eine Schädigung beschleunigt.
Soll durch eine Beschichtung die Qualität der Bodenoberfläche erhöht werden, ist eine einwandfreie Haftung der Beschichtung zum Untergrund sicherzustellen, um mechanische Einwirkungen abzuleiten. Vor allem Scherbeanspruchungen können sonst durch einen „Walkeffekt“ zu einer Delamination führen. Diese Versagensart wird durch eine optimale Untergrundvorbehandlung sicher vermieden. Das Ziel jeder Untergrundvorbehandlung, z. B. durch Fräsen, Schleifen oder staubfreies Kugelstrahlen, ist eine porentief geöffnete Oberfläche. So wird eine optimale mechanische Verkrallung ermöglicht.
Daneben sind vor allem die durch die Hersteller vorgegebenen Verarbeitungsbedingungen einzuhalten. Mindestfestigkeit, Oberflächenzugfestigkeit, Mischprozedere, Feuchtegehalt des Untergrundes und der Luft sowie der zulässige Temperaturbereich von Material, Luft und Untergrund sind dabei entscheidende Faktoren.
Spezielle Systemeigenschaften
Grundsätzlich unterscheidet man mechanische, chemische und thermische Beanspruchungen, die ein Bodenbeschichtungssystem dauerhaft bewältigen muss. Bei mechanischen Belastungen kann weiter unterschieden werden in reibende oder abrasive Belastungen (z. B. durch das Schieben einer Palette über den Boden), Druck (z. B. gelagerte Ware) und plötzliche Schlageinwirkung (z. B. durch herunterfallende Gegenstände). Da die Bandbreite der möglichen chemischen Substanzen – zu nennen sind hier organische und anorganische Säuren, Laugen, Lösemittel etc. – enorm ist, müssen Bodenbeschichtungen besonders sorgfältig auf die zu erwartenden chemischen Beanspruchungen angepasst werden. Eine schnelle und zuverlässige Hilfestellung bieten die Hersteller mit ihren Sicher-heitsdatenblättern. Daneben müssen unbedingt auch andere Faktoren wie z. B. die Beaufschlagungsintervalle und Kombinationen aus unter-schiedlichen Medien berücksichtigt werden. Reaktionsharzprodukte können bei hohen Temperaturen ihre Eigenschaften verändern oder sogar verlieren. Abhängig vom Glasübergangsbereich der unterschiedlichen Systeme liegt die maximal mögliche dauerhafte Temperaturbeaufschlagung bei 65 bis 110 °C. Dabei ist eine trockene Hitze z. B. durch Öfen besser zu kompensieren als nasse Hitze z. B. durch Kochwasser bei Tankreinigungsanlagen oder häufiger Dampfreinigung.
Die Faktoren dürfen aber nicht isoliert betrachtet werden, sondern es sind auch alle möglichen Kombinationen zu berücksichtigen, auch in Hinblick auf eine spätere Umnutzung. Spitzentemperaturen, die Geschwindigkeit der Temperaturänderung, die Belastungsintervalle, die Dauer der Belastung, Chemikalien, die erhitzt möglicherweise deutlich aggressiver wirken oder zusätzliche Drücke müssen im Vorfeld geklärt werden. Die Wahl des Beschichtungsmaterials wird auch dadurch beeinflusst, ob ein potentielles einmaliges Havarieereignis abgedeckt werden muss, bei dem die Beschichtung notfalls sogar eine Opferschicht darstellt, oder ob es sich um eine gelegentliche Spritzbelastung handelt.
Industrieböden oder Werksstraßen bzw. Freiflächen werden im Gegensatz zu öffentlichen Straßen durch geringeres Verkehrsaufkommen und niedrigere Geschwindigkeiten (< 30 km/h), aber teilweise hohe Punktlasten durch Gabelstapler oder Regalsysteme beansprucht. Während Betonböden in geschlossenen Hallen weitgehend frei von äußeren Temperaturbeanspruchungen sind, müssen Freiflächen Temperaturschwankungen sowie einem Frost- und Taumittel-Angriff standhalten.
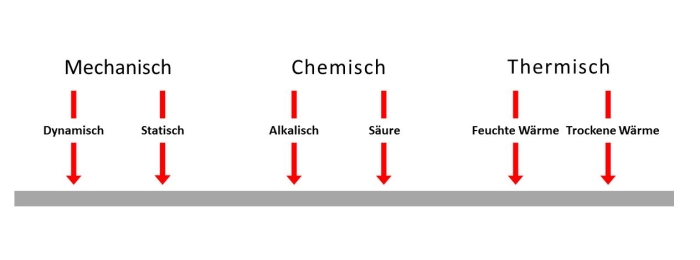
Der mechanische Belastungsgrad durch Abrasion kann für Beton- und Estrichoberflächen durch den Verschleißwiderstand vorgegeben und geprüft werden. In Deutschland wurde der Verschleißwiderstand bisher nach DIN 52108 (Schleifverschleiß nach Böhme) bestimmt. In der europäischen Estrichnorm DIN EN 13813 sind neben dem Verfahren nach Böhme (siehe Tabelle 1) auch Verschleißwiderstandsklassen für zwei weitere Verfahren – nach BCA (British Cement Association) und gegen Rollbeanspruchung – aufgenommen.
Klasse | A22 | A15 | A12 | A9 | A6 | A3 | A1,5 |
Abriebmenge [cm³/50 cm²] | 22 | 15 | 12 | 9 | 6 | 3 | 1,5 |
Tabelle 1: Verschleißwiderstandsklassen nach DIN EN 13813 (Verfahren nach Böhme) |
Neben den Basisbelastungsarten (siehe Abbildung 1) gibt es darüber hinaus eine sehr große Anzahl an weiteren Eigenschaften, die individuell auf die Bedingungen vor Ort abzustimmen sind. Neben rein technischen Anforderungen, wie z. B. Rissüberbrückung, Diffusionsfähigkeit, Rutschhemmung, Ableitfähigkeit, Brandverhalten, spielen zunehmend eine ganze Reihe weiterer Faktoren eine Rolle: Neben Design und Optik hat das Thema Umweltschutz und Gesundheit des Nutzers in den letzten Jahren sehr stark an Bedeutung gewonnen, wie z. B. physiologische Unbedenklichkeit, Dekontaminierbarkeit, ökologische Produktion oder die REACh-Bewertung nach dem neuen europäischen Chemikaliengesetz. Zukünftig werden auch Aspekte der Nachhaltigkeit eine größere Rolle spielen. Für den Nutzer ergibt sich aus dieser Bandbreite eine individuelle Lösung für seine Bodenflächen, wobei es durchaus Faktoren gibt, die sich gegenseitig ausschließen, wie z. B. eine hohe Rutschhemmung und optimale Reinigungsfähigkeit.
Vorteile eines reaktionsharzbeschichteten Industriebodens
Da mineralische Systeme häufig gewisse Grenzen besonders im Hinblick auf die Chemikalienbeständigkeit sowie Verschleißfestigkeit vorweisen, stellt der Industriefußboden, der mit einem Reaktionsharz beschichtet wird, eine gute Alternative dar. Diese Industrieböden bieten gegenüber mineralischen Systemen viele Vorteile. Sie verfügen über eine längere Lebensdauer als herkömmliche Fußböden, können absolut fugenlos verlegt werden und sind schlag-, kratz- und stoßfest. Durch ihre völlig glatte Oberfläche sind sie auch unter schwierigen hygienischen Gegebenheiten problemlos sauber zu halten. Sie sind in erhöhtem Maß beständig gegen eine Vielzahl von Chemikalien, unempfindlich gegen Temperaturschwankungen, die z. B. in lebensmittelverarbeitenden Betrieben auftreten können, halten auch hohem Druck problemlos stand und verfügen durch ihre hohe Festigkeit über einen extrem hohen Abriebwiderstand. Bei diesen Industrieböden kommen reaktionsharz-basierte Flüssigkunststoffe zum Einsatz. Diese bestehen je nach Verwendung aus Epoxidharzen, Polyurethanharzen oder PMMA-Harzen.
Reaktionsharzbasierte Flüssigkunststoffe werden als 1-, 2- oder Mehr-Komponenten-Produkt eingesetzt. Ihre Verarbeitung erfolgt nach grundlegender Untergrundvorbereitung mit verschiedenen Werkzeugen wie z. B. Fellwalzen oder Rakeln. Während 1K-Produkte in der Regel durch die Luftberührung verfilmen, findet bei 2K- und Mehr-Komponenten-Produkten eine chemische Reaktion von Basisharz und Härter (ggf. Katalysator) im Flüssigkunststoff statt. Nach einer gewissen Reaktionszeit härtet der Flüssigkunststoff aus und dichtet so Flächen und Details nahtlos ab. Die Flüssigkunststoff-Harztypen besitzen verschiedene grundsätzliche Eigenschaften. Allgemein lässt sich sagen, dass ein Flüssigkunststoff auf Basis von PMMA besonders schnell reagiert, Epoxidharze sich durch ihre hohe mechanische wie auch chemische Beständigkeit auszeichnen, während Polyurethane oftmals elastische Eigenschaften zeigen.
Reaktionsharzbasierte Flüssigkunststoffe sind daher sehr vielseitig einsetzbar. So sind Dekor- und Designböden bis hin zu extrem strapazierfähigen und chemikalienbeständigen Industrieböden möglich, von glatt bis strukturiert oder rutschsicher.
Highspeed-Beschichtungssystem
In den vergangenen Jahren sind weitere Innovationen dazugekommen, wie z. B. ein Highspeed-Beschichtungssystem der MC-Bauchemie, das auf modifiziertem Polyurethan basiert und Beschichtungsarbeiten auch bei kritischen Umgebungsbedingungen von 2 bis 35 °C und Nässe ermöglicht. Im Gegensatz zu gängigen Bodenbeschichtungen auf Polyurethan- und Epoxidharzbasis, die sich in der Regel nur zwischen 8 und 30 °C verarbeiten lassen und bei kühleren Temperaturen, Umgebungsfeuchtigkeit und Nässe unerwünschte Nebenreaktionen wie Haftungsstörungen, Blasen, Krater und Poren sowie lange Aushärtezeiten zeigen, beschleunigen Feuchtigkeit und Nässe den Erhärtungsprozess dieser neuen Highspeedbeschichtung und steigern Haftung, Abriebwiderstand und Kratzfestigkeit noch zusätzlich. Vollständige Industrieböden können innerhalb weniger Stunden aufgebaut und nach 48 Stunden wieder voll belastet werden. Das Beschichtungssystem der MC-Bauchemie nutzt eine spezielle Werkstofftechnologie, die aus dem Kraftwerksbau stammt und die auf Bodenbeschichtungen im Innen- und Außenbereich adaptiert wurde. Sie wird in der Industrie, besonders in der Lebensmittelindustrie und in Großküchen, genauso wie im Ladenbau oder auch im klassischen Wohnungsbau wie z. B. auf Balkonen, Laubengängen und Terrassen oder Garagen und vielen weiteren Flächen angewandt.
Die Rutschhemmung
Eine der am häufigsten geforderten Eigenschaften für Boden-beschichtungssysteme ist die Rutschhemmung, da Sturz- und Stolperunfälle auch heute noch an der Spitze der Betriebsunfallstatistiken stehen. Insbesondere glatte Oberflächen, Verschmutzungen und flüssige Medien als gleitfördernde „Schicht“ erhöhen die Gefahr des (Aus)Rutschens.
Rutschhemmung wird bei kunststoffbasierten Beschichtungssystemen erreicht, indem auf die bereits ausgehärtete Kratzspachtelung vorgefülltes pigmentiertes Harz vorgelegt wird und die noch frische Oberfläche mit Sand im Überschuss abgestreut wird. Der Sand sinkt teilweise in das Harz ein und wird während des Erhärtungsvorgangs des Bindemittelharzes dauerhaft eingebunden. Am Folgetag wird der lose nicht eingebundene Sand auf der Beschichtungsoberfläche entfernt. Die Oberfläche besitzt nun durch den eingebundenen Sand eine definierte Rauigkeit. Abschließend wird eine pigmentierte Kopfversiegelung aufgerollt, die Oberfläche ist nun dicht und farbig, dennoch bleibt die Rauigkeit der Sandeinstreuung erhalten. Die Rauigkeit kann durch die Wahl der Körnung stark beeinflusst werden. Je gröber der Sand ist, desto stärker ist die Rauigkeit der Oberfläche. Im Allgemeinen werden Sande der Körnung 0,2 bis 0,7 mm verwendet.
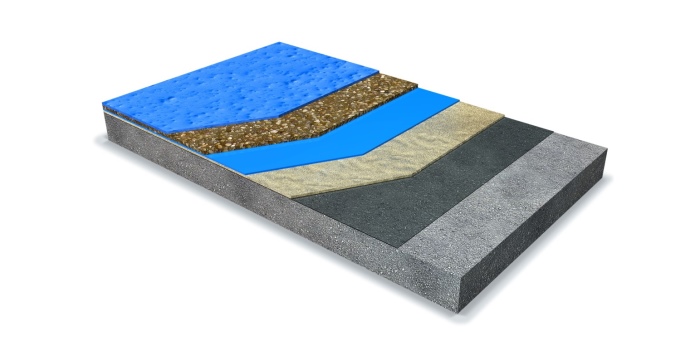
Die Rauigkeit des Untergrundes, die letztendlich die Rutschhemmung gewährleistet, steht im Widerspruch zu anderen durchaus wichtigen Eigenschaften des Beschichtungssystems. So sinkt mit zunehmender Rauigkeit die Reinigungsfähigkeit deutlich ab, weil sich Schmutzpartikel besser festsetzen können und mit manuellen oder maschinellen Reinigungsverfahren nur mit erhöhtem Aufwand zu entfernen sind. Darüber hinaus sinkt auch der Gehkomfort, da die Auftrittsfläche nur durch die Kornspitzen gebildet wird. Auch andere Eigenschaften wie Rissüberbrückung oder Diffusionsfähigkeit werden durch die Rauigkeit beeinflusst. Hier ist häufig eine sachkundige Beratung zur Findung eines sinnvollen Kompromisses notwendig. Eine gewisse Rutschhemmung kann auch über das leichte Einstreuen von dekorativen Kunststoff-flocken oder das Einrollen von Glasperlen in glatte Oberflächen erzielt werden.
Die Prüfung der Rutschhemmung wird auf der „schiefen Ebene“ nach DIN 51130 „Prüfung von Bodenbelägen; Bestimmung der rutschhemmenden Eigenschaft“ ermittelt. Dabei geht eine Prüfperson über ein Muster des zu prüfenden Belags, dessen Neigung soweit vergrößert wird, bis die Prüfperson ein subjektiv unsicheres Gefühl während des Gehens empfindet oder tatsächlich abrutscht und durch ein Trägersystem aufgefangen wird. Der Bodenbelag wird zuvor mit Motorenöl als gleitförderndes Mittel versehen, des Weiteren werden definierte Schuhsohlen verwendet. Nach der BGR 181 „Fußböden in Arbeitsräumen und Arbeitsbereichen mit Rutschgefahr“ wird bei einem mittleren Neigungswinkel von mindestens 6° der Bodenbelag der Bewertungsgruppe R 9 zugeordnet, die gestaffelt bis zu R 13 bei einem Winkel größer 35° steigen kann. R 9 entspricht somit einer leichten, R 13 einer sehr hohen Rutschhemmung. Zusätzlich kann bei großen Rauigkeiten der Verdrängungsraum ermittelt werden, der den aufsummierten Hohlraum zwischen der Sohle und der Beschichtung bezeichnet und von V 4 (> 4cm3/dm2) bis V 10 (>10cm3/dm2) gestaffelt ist (siehe Tabelle 2).
Bewertungsgruppe | Akzeptanzwinkel | Verdrängungsraum | Mindestvolumen |
R 9 | 6° bis 10° | V 4 | 4 cm³/dm² |
R 10 | >10° bis 19° | V 6 | 6 cm³/dm² |
R 11 | >19° bis 27° | V 8 | 8 cm³/dm² |
R 12 | >27° bis 35° | V 10 | 10 cm³/dm² |
R 13 | > 35° | ||
Tabelle 2: BIA-Bewertungsgruppen |
Obwohl diese Prüfung sich in Deutschland weitgehend etabliert hat, ist sie dennoch nicht unumstritten. Die Klassifizierung der Bodenbeläge bezieht sich durch die Verwendung von Öl als gleitförderndes Mittel immer auf den worst-case, der z. B. in Schulklassen oder Einzelhandelsbereichen nie erreicht wird. Außerdem hat das Sicherheitsbewusstsein dazu geführt, dass häufig auch für permanent trockene Bereiche eine Rutschhemmungsklasse gefordert wird, die aber ausdrücklich gar nicht unter den Anwendungsbereich der BGR 181 fallen. Dies führt häufig zu einem „mit Kanonen auf Spatzen“-Ansatz. Schließlich ist die Bewertung im Rahmen der Laborprüfung mit einer schiefen Ebene auch immer bis zu einem gewissen Grad subjektiv.
Es existieren auch international eine ganze Reihe weiterer Prüfmethoden, keine hat sich allerdings bislang durchgesetzt, was an den vergleichsweise hohen Kosten liegt und an der noch fehlenden Korrelation untereinander.
Die Ableitfähigkeit
Bei dem Kontakt zweier schlecht leitender Materialien (Isolatoren) findet eine Ladungstrennung statt, was einen elektronischen Potentialunterschied zur Folge hat. Auch schon bei leichten Reibvorgängen kann dabei ein Potentialunterschied von mehreren tausend Volt entstehen. Die Höhe der Aufladung hängt stark von der umgebenden Luftfeuchtigkeit ab, je geringer, desto höher die Ladungstrennung. Ab einem Potentialunterschied von ca. 3000 Volt ist ein Mensch in der Lage die Entladung zu spüren. Dies ist z. B. der Fall, wenn einem nach dem Ausziehen eines Kunstfaserpullovers „die Haare zu Berge“ stehen oder man ein unangenehmes Kribbeln beim Berühren einer Türklinke oder einer Autokarosserie spürt. Auch Blitze während eines Gewitters sind eine solche plötzliche Entladung. Im industriellen Bereich kommen solche Vorgänge durch Reibung, Zerkleinerung oder Mahlen vor. Die dabei auftretenden plötzlichen Entladungen können mikroelektronische Bauteile bereits ab 100 V schädigen, also deutlich unter der für den Menschen spürbaren Schwelle und daher weitgehend unbemerkt. Allerdings ergeben sich daraus häufig Schäden an den Bauteilen, die sich dann im Rahmen der Qualitätssicherung zeigen oder latente Schäden, die erst bei der Benutzung und Belastung der Halbleiter sichtbar werden. In vielen Bereichen, wie z. B. der Airbag-Elektronik können die Folgen erheblich sein. Die Ausfallkosten in der Elektronikindustrie durch „electrostatic-discharge“ (ESD) sind enorm.
Aber auch in Bereichen, in denen sich eine explosive Atmosphäre bilden kann, sei es durch Gase, Dämpfe oder Stäube, sind Funkenentladungen unbedingt sicher zu vermeiden. Diese Anforderung ist in einer Reihe von gesetzlichen Vorschriften verankert (Betriebs-Sicherheitsverordnung, Technische Regeln für brennbare Flüssigkeiten). Für beide Fälle gibt es nur die Möglichkeit statt der normalerweise isolierenden Boden-beschichtungen (wie auch Beton) definiert ableitfähige Bodenbeschichtungssysteme zu applizieren, die eine statische Aufladung wirksam verhindern. Im Allgemeinen gilt ein Erdableitwiderstand von 10^8 Ohm, bei der Lagerung von Explosivstoffen müssen 10^6 Ohm unterschritten werden. In „electrostatic protected areas“, den so genannten EPAs, ist zum Schutz besonders empfindlicher mikro-elektronischer Bauteile zusätzlich der Systemwiderstand „Mensch-Schuh-Boden“ nachzuweisen sowie eine maximale Körperaufladung des Systems „Mensch-Schuh-Boden“ von 100 V.
Die Ableitfähigkeit des Bodenbeschichtungssystems wird normalerweise durch die Zugabe von leitfähigen Fasern erreicht, die eine vertikale Ableitung durch die Deckschicht ermöglichen. Darunter ist eine dünne, horizontal leitende Spezialgrundierung appliziert. Diese wiederum leitet die Spannung zu einem Kupferleitband, was in einem regelmäßigen Leitraster auf die Kratzspachtelung appliziert wurde, und schließlich über einen Erdungspunkt an die Gebäudeerde.
Optik und Design
Außergewöhnliche und optisch ansprechende Böden werten den Gesamteindruck einer Immobilie auf. Und mit reaktionsharzbasierten Bodenbeschichtungssystemen sind die Möglichkeiten zur Oberflächen-gestaltung enorm vielfältig. Eine sehr einfache Methode ist das leichte Einstreuen von farbgebenden Dekorflakes, Kunststoffflocken, die in einer sehr großen Farbauswahl erhältlich sind. Eine weit verbreitete Methode ist auch, statt einer Einstreuung aus Quarzsand einen gecoateten farbigen Dekorquarzsand vollsatt einzustreuen und schließlich zum Schutz transparent zu versiegeln, so dass der Blick des Betrachters durch die transparente Versiegelung auf die farblich strukturierenden Körnungen fällt. Alternativ können auch die Dekorflakes vollsatt eingestreut und transparent versiegelt werden.
Zusammenfassung
Heutzutage müssen moderne Bodenbeschichtungssysteme eine große Fülle an unterschiedlichen Anforderungen erfüllen, die neben technischen auch optisch-ästhetische und gesundheitsrelevante Aspekte beinhalten. Die Materialien sind dabei immer im Zusammenhang mit den vor Ort herrschenden Gegebenheiten zu betrachten. Reaktionsharzbasierte Bodenbeschichtungssysteme stellen aber eine gute Alternative zu mineralischen Systemen dar, da sie absolut fugenlos verlegt werden können und schlag-, kratz- und stoßfester sind. Durch ihre völlig glatte Oberfläche sind sie auch unter schwierigen hygienischen Gegebenheiten problemlos sauber zu halten. Sie sind unempfindlich gegen alle Temperaturschwankungen, halten auch hohem Druck und chemischen Beanspruchungen stand und verfügen durch ihre hohe Festigkeit über einen extrem hohen Abriebwiderstand. Sie haben auch eine wesentlich längere Lebensdauer als herkömmliche Fußböden.
Nur eine sorgfältige Abstimmung und eine fundierte Beratung sowie eine fachgerechte Verlegung sichern jedoch erst den dauerhaften Erfolg einer Beschichtungsmaßnahme.
[tabs]
[tab title=“Die Autorin“]Dr. Patricia Steffen
Product Manager Flooring Systems bei MC-Bauchemie Müller GmbH & Co. KG[/tab]
[/tabs]